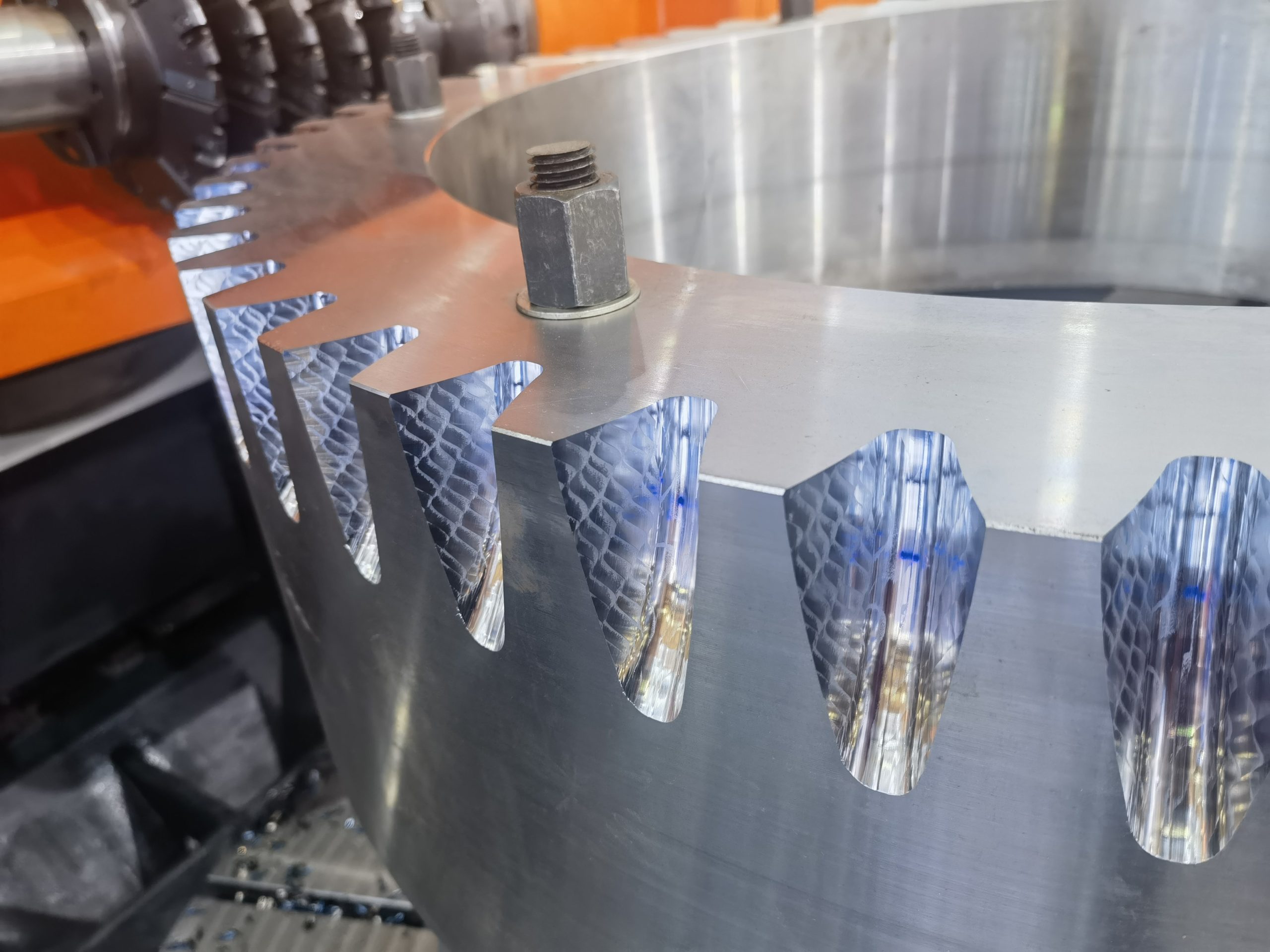
High-efficiency hobbing and milling machine tool
With the advancement of machine tool manufacturing technology and tool technology, the high-efficiency rolling and milling compound machine has broken the traditional understanding of gear hobbing machines, with cutting efficiency several times that of traditional gear hobbing machines. Compared to high-speed gear milling machines, the high-efficiency rolling and milling compound machine has the following advantages in addition to directly installing disk milling cutters to complete gear milling processing: 1) Gear hobbing uses the involute method for processing, with continuous indexing and higher precision than gear milling; 2) Gear hobbing has better centering performance, as the vibration of the cutter during gear milling will cause certain offset, and the gear processed is not absolutely centered; 3) In the high-speed gear hobbing process, multiple rows of cutting edges participate in cutting, resulting in less cutter impact and wear, especially in the precision finishing process. The wear of gear milling cutters can cause local stress concentration during heat treatment, leading to broken teeth; 4) In terms of efficiency, both gear hobbing and gear milling are high-efficiency cutting processes. The efficiency of gear processing at the same module is related to the number of teeth. Below a certain value, gear milling efficiency is higher than gear hobbing, while above a certain specific value, the more the number of teeth, the higher the gear hobbing efficiency. After choosing a high-efficiency rolling and milling compound machine, customers can make better choices based on production volume and precision; 5) Equipped with rolling and milling compound functions: the machine tool tool holder has a large transverse space, allowing for the simultaneous installation of milling cutters and hob cutters. For some gears, a rough milling + precision rolling one-time processing technology can be adopted, achieving a perfect combination of efficiency, cost, and precision.
一、产品优势
1. High-rigidity linear shaft transmission: The X-axis and Z-axis use integral steel guide rail (non-jointed) and INA rolling elements, ensuring that the machine tool has no clearance in the movement of its components during the cutting process. The steel guide rail is ground using a world-class guide rail grinding machine, with a straightness of ≤0.005mm/1000mm and parallel and perpendicular accuracy of ≤0.015mm. With the application of INA rolling elements, high-precision gapless rolling transmission is achieved, ensuring the high rigidity, high precision, and stability of the X-axis and Z-axis during the cutting process.
2. High-rigidity, high-precision worktable: 1) The design ensures sufficient rotational rigidity and eliminates return clearance by selecting a double worm gear structure with larger diameter and module, and higher precision; the end face and radial support adopt internationally advanced constant current hydrostatic structure, ensuring the high rigidity and high precision of the worktable; 2) In terms of technology, the worktable worm is processed by an imported worm gear machine, with adjacent worm gear precision Fu stable at national standard level 1, and cumulative precision at level 3; 3) Precision scraping and finishing process: The static pressure support surface and the end face of the worm gear bracket both adopt precision scraping and finishing process, with high flatness and good static pressure support rigidity.
3. High-rigidity spindle box: 1) The hob frame parts use the servo spindle motor to drive the gear secondary transmission, and a special gear sub-gap removal structure is designed to eliminate the transmission gap, reduce the mechanical vibration noise caused by the transmission gap and intermittent cutting force of the machine tool during the processing process, and improve the machining accuracy of the machine tool and Efficiency; 2) The tool spindle is radially supported by high-precision heavy-duty cylindrical roller bearings, and the heavy-duty end cylindrical roller bearings for axial support, and the adjustment mechanism is designed to accurately adjust the gap value and preload of each bearing to obtain high support rigidity and accuracy. The spindle jumps within 0.005mm; 3) Hob frame The design of the enlarged tool diameter can be installed with a large diameter that can be converted into a hob and a disc milling cutter for dry cutting. After the knife mechanism and the knife holder turn the angle in place, a special mechanical automatic locking and loosening mechanism is designed, which is convenient for operation. 4) The machine tool adopts a high-rigidity bracket structure, arc support, good support rigidity, convenient disassembly, especially suitable for large modulus cutting; 5) The spindle interface adopts an automatic locking mechanism, and the tool tightening device adopts hydraulic lock female automatic locking, which is convenient to disassemble the tool and can protect the spindle; 6) The spindle box gear tooth shape and tooth direction are repaired. Type design and processing, the gearbox impact is small, the transmission is stable, and the stability is high.
4. High-efficiency dual hydraulic station provides power: All clamping and loosening of the machine tool adopts Japanese Fujikoshi hydraulic unit, and the static pressure and lubrication of the workbench are controlled by independent hydraulic station. The unique dual hydraulic station design ensures the cleanliness of the oil, the accuracy and reliability of the action, reduces the heat generation of the hydraulic station, greatly improves the reliability and stability of hydraulic control and saves energy consumption.
5. Powerful digital control technology: 1) The machine tool is equipped with the functions of power failure and emergency rollback, which ensures that the tool can be exited in abnormal cases without damaging the tool; 2) It is equipped with processing software such as hobbing teeth, milling teeth, drum teeth, etc., which can easily realize gear processing of various processes; 3) Customers can choose the 828D and 840Dsl systems according to their own needs; 4) The machine tool control logic is strict, and it will immediately alarm and stop in case of over-range, overload, pressure loss and other faults to ensure the safety of human and machine.
6. Excellent machine tool performance: the processing performance of the machine tool is excellent, and the processing accuracy and efficiency are comparable to those of foreign counterparts in the United States. The number of transpositionable hob processing modules is 18.7 wind power planetary gears, the one-knife hobbing accuracy is level 6 national standard, and the two-knife hobbing processing accuracy is level 4. Milling tooth processing 14 modules one knife milling accuracy national standard level 7.
Specifications
Project/Model | GH600 | GH800 | GH1250 | GH2000 | GH3000 | GH4000 | GH5000 | GH6000 |
Workpiece diameter (mm) | 600 | 800 | 1600 | 2500 | 3500 | 4500 | 5500 | 6500 |
Maximum modulus (mm) | 16 | 16/30 | 20/30 | 30 | 30 | 30/40 | 40 | 40 |
Maximum axial stroke (mm) | 800 | 800/1300 | 1300 | 1300/1700 | 1000/1700 | 1200/2000 | 1200/2000 | 1200/2500 |
工作台面直径mm | 600 | 800 | 1250 | 2000 | 2600 | 3200 | 4000 | 4800 |
Workbench speed min- | 25/40 | 25 | 12 | 10 | 10 | 7 | 5 | 5 |
Minimum distance between lathe/workbench center (mm) | 0 | 0 | 0 | 300 | 650 | 900 | 900 | 900 |
Rotation Angle ° | ±45 | ±45 | ±45 | ±45 | ±45 | ±45 | ±45 | ±45 |
Rolling die shaft positioning | HSK100 | HSK125 | HSK125 | BT60/HSK160 | BT60/HSK160 | HSK160 | HSK160 | HSK160 |
Maximum string knife/tang travel (mm) | 240 | 320 | 320 | 320 | 320 | 320 | 320 | 320 |
Maximum Roll Cutter Diameter | 260 | 450 | 450 | 450 | 450 | 500 | 500 | 500 |
Maximum Roll Cutter Length | 300 | 430 | 605 | 605 | 700 | 700 | 700 | 700 |
Rolling cutter speed | 360 | 300 | 240 | 240 | 240 | 240 | 240 | 240 |
Spindle Power (Kw) | 32 | 37.5/67.5 | 45/67.5 | 67.5 | 67.5 | 67.5 | 80 | 80 |
Machine tool weight (tons) | 约18 | 约25 | About 35 | 约45 | 约50 | 约55 | 约70 | 约85 |
Total power(Kw) | 60 | 65 | 70 | 80 | 80 | 90 | 100 | 110 |